Introduction
Crane trucks play a crucial role in various industries, from construction to logistics and beyond. These powerful machines are capable of lifting and moving heavy loads, making them indispensable in many operations. However, operating a crane truck comes with inherent risks, especially when dealing with heavy loads and complex lifting scenarios. To mitigate these risks and enhance safety and efficiency, crane truck load moment indicators have become essential tools for crane operators and construction professionals. In this article, we will delve into the world of crane truck load moment indicators, exploring their importance, functionality, benefits, and best practices for their use.
Importance of Load Moment Indicators
Load moment indicators (LMIs) are devices designed to monitor and display key data related to the load being lifted by a crane truck. This includes information such as the load weight, boom angle, and load radius. By providing real-time feedback on these critical parameters, LMIs help crane operators make informed decisions and prevent overloading, tipping, or other dangerous situations.
The primary importance of load moment indicators can be summarized as follows:
1. Safety: The most crucial aspect of load moment indicators is their role in enhancing safety on the job site. By alerting operators to potential overload situations or unsafe lifting conditions, LMIs help prevent accidents and injuries.
2. Efficiency: In addition to safety, load moment indicators also contribute to operational efficiency. By providing accurate load weight information and other relevant data, LMIs enable operators to optimize their lifting operations and work more efficiently.
3. Compliance: Many regulatory bodies and industry standards require the use of load moment indicators on crane trucks to ensure compliance with safety regulations. By using an LMI, operators can demonstrate their commitment to safety and regulatory compliance.
Functionality of Load Moment Indicators
Load moment indicators come in various forms and configurations, but they all share a common set of key features and functionalities. The primary components of an LMI system include sensors, a central processing unit (CPU), a display unit, and an alarm system. Let's explore each of these components in more detail:
1. Sensors: Sensors are the heart of any load moment indicator system. These devices are responsible for measuring key parameters such as load weight, boom angle, and load radius. Common types of sensors used in LMIs include load cells, inclinometers, and distance sensors.
2. Central Processing Unit (CPU): The CPU is the brain of the LMI system, responsible for processing the data collected by the sensors and calculating the load moment. The CPU also controls the operation of the LMI and communicates with the display unit and alarm system.
3. Display Unit: The display unit is where the operator can view the real-time data provided by the LMI system. This includes information such as load weight, boom angle, load radius, and any relevant alerts or warnings. The display unit is typically mounted in the crane cab for easy visibility.
4. Alarm System: The alarm system is a critical safety feature of load moment indicators. If the LMI detects an overload or unsafe condition, it will trigger an alarm to alert the operator. This could be an audible alarm, visual alert, or both, depending on the specific LMI system.
Benefits of Load Moment Indicators
The use of load moment indicators offers a wide range of benefits for crane operators and construction professionals. Some of the key advantages of using LMIs include:
1. Enhanced Safety: The most significant benefit of load moment indicators is the improvement in safety on the job site. By providing real-time feedback on load conditions and potential risks, LMIs help prevent accidents and injuries caused by overloading or unstable lifting operations.
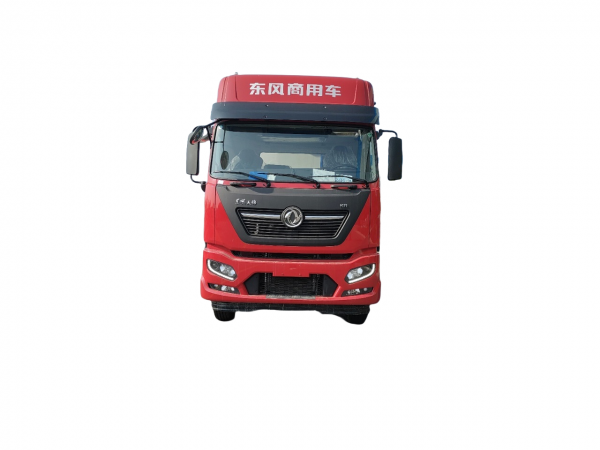
2. Increased Productivity: LMIs enable operators to work more efficiently by providing accurate load weight information and other critical data. This allows operators to optimize their lifting operations, minimize downtime, and complete tasks more quickly.
3. Reduced Risk of Damage: Overloading a crane truck can lead to equipment damage, structural failures, and costly repairs. Load moment indicators help prevent overloading by alerting operators to unsafe conditions, reducing the risk of damage to the crane and its surroundings.
4. Regulatory Compliance: Many industry standards and regulations require the use of load moment indicators on crane trucks to ensure safe operations. By using an LMI, operators can comply with these requirements and demonstrate their commitment to safety and compliance.
Best Practices for Using Load Moment Indicators
To maximize the benefits of load moment indicators and ensure safe and efficient crane truck operations, operators should follow best practices for using LMIs. Some key best practices include:
1. Regular Calibration: It is essential to calibrate the load moment indicator system regularly to ensure accurate readings. Calibration should be performed by qualified technicians using proper equipment and procedures.
2. Truck Mounted Crane customizations : Proper training is crucial for crane operators to understand how to use the load moment indicator effectively. Operators should be familiar with the LMI system, its features, and how to interpret the data provided.
3. Pre-Operation Checks: Before each lifting operation, operators should perform pre-operation checks to ensure that the load moment indicator system is functioning correctly. This includes verifying sensor readings, alarm systems, and display unit visibility.
4. Monitor Load Conditions: Throughout the lifting operation, operators should continuously monitor load conditions and LMI data to detect any changes or potential risks. Operators should be prepared to respond quickly to any alarms or warnings from the LMI system.
Conclusion
Crane truck load moment indicators are invaluable tools for enhancing safety, efficiency, and compliance in crane operations. By providing real-time data on load weight, boom angle, and other critical parameters, LMIs help prevent accidents, optimize lifting operations, and ensure regulatory compliance. To make the most of load moment indicators, operators should follow best practices for their use, including regular calibration, operator training, pre-operation checks, and continuous monitoring of load conditions. With the right approach and attention to detail, crane operators can harness the power of load moment indicators to safely and effectively carry out their lifting tasks.